
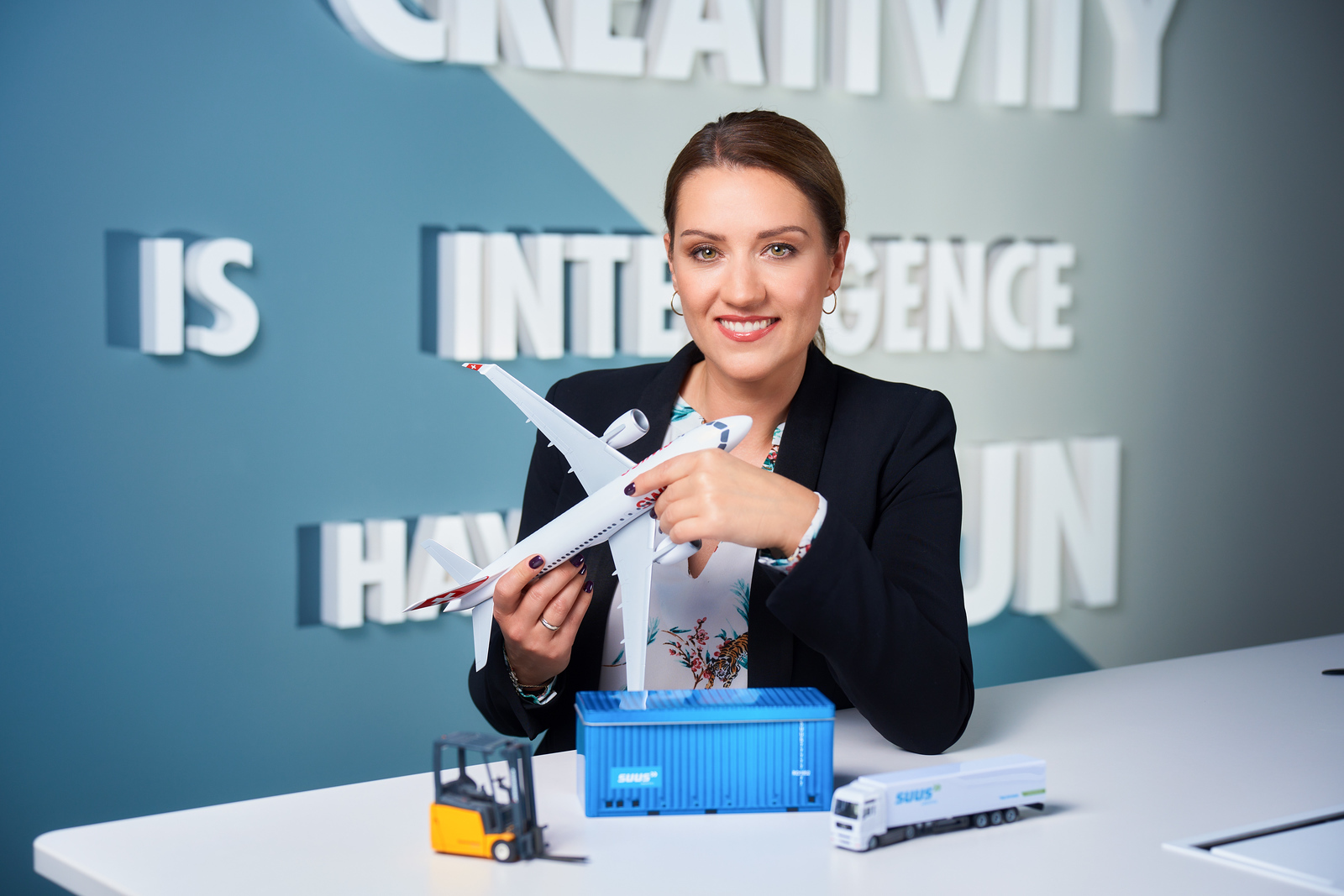
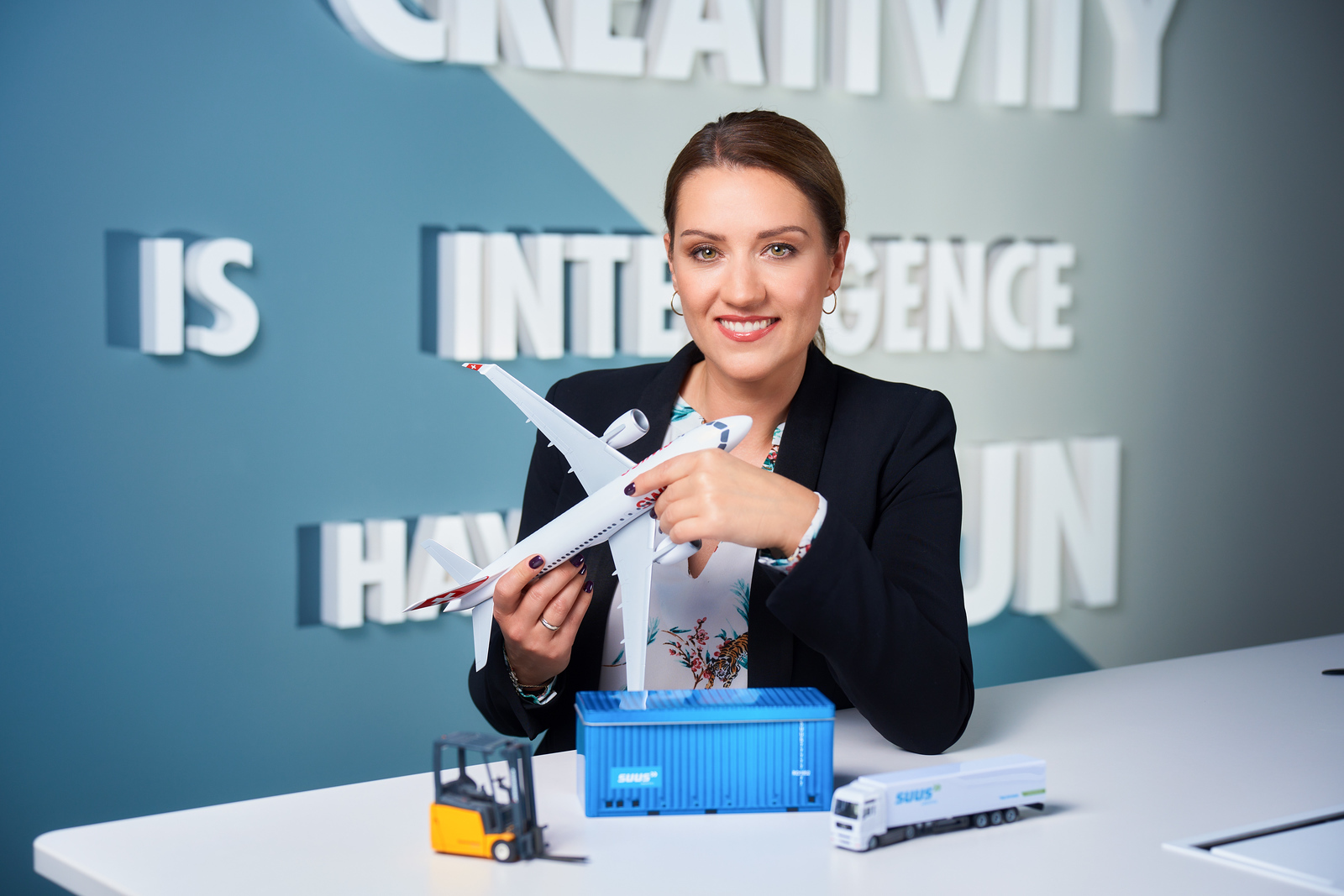
How to design supply chains to tackle today’s market challenges? Aleksandra Gumel, Head of Logistics Solution Design CEE at Rohlig SUUS Logistics
Markets seem to have stabilized after the pandemic and the outbreak of war in Ukraine. Have companies already found their footing in the new reality?
On the one hand, we can see that the situation after the COVID-19 pandemic or the outbreak of war in Ukraine has stabilized to some extent, e.g. rates in sea freight have fallen back to pre-pandemic times. On the other hand, we are facing an economic slowdown, which naturally affects one industry less and another one more. The last few years of turmoil have changed the strategies of many companies. More and more of them are learning this new reality, changing their business approach, so that they will be ready for any difficulties yet to come. Therefore, in logistics, more and more attention is being paid to building resilient supply chains that will ensure continuity of supply or distribution at the time of an unexpected crisis.
What is influencing supply chain decisions the most right now?
Certainly, the cost of transport and the rates on individual freight are still an important factor. However, we are noticing that companies are increasingly focusing on sustainability in their operations, which we at SUUS are particularly pleased about, as we believe that logistics can and should be increasingly green and responsible. Compared to last year, there has been an increase in the number of enquiries about designing logistics solutions that contribute to reducing the carbon footprint. These changes are being driven by, among other things, regulations being introduced in this area (e.g. the Fit for 55 package) or consumer trends forcing manufacturers to implement sustainable solutions.
The aforementioned security of the entire supply chain is also an important decision-making factor. Some companies rely on stock building in this aspect, while others, for example, turn to diversification of sales or supply markets, e.g. through nearshoring or reshoring. A report by Maersk and Reuter Events last year found that 67% of global retailers and manufacturers said that disruptions in the global supply chain have forced them to change the source of their materials and components. Moreover, Poland is cited as the most attractive location among European businesses. At SUUS, we also notice this trend. As part of our Project Cargo service we even help customers relocate entire production lines. It is also worth noting that nearshoring is also a way of building greener supply chains, as a shorter supply chain is also an opportunity to reduce the carbon footprint.
Chart: Most attractive locations for nearshoring or reshoring – respondents’ indications (European companies)

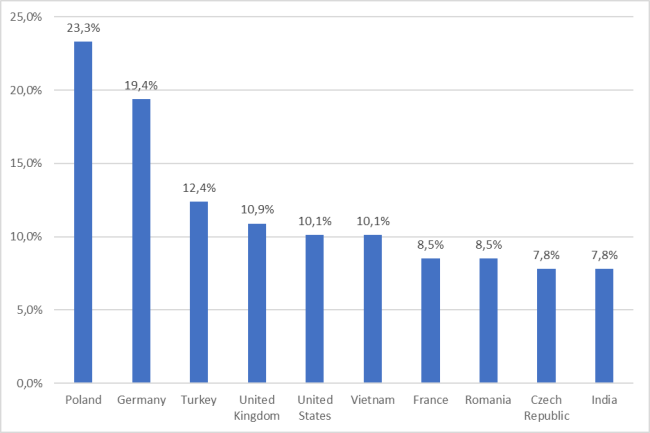
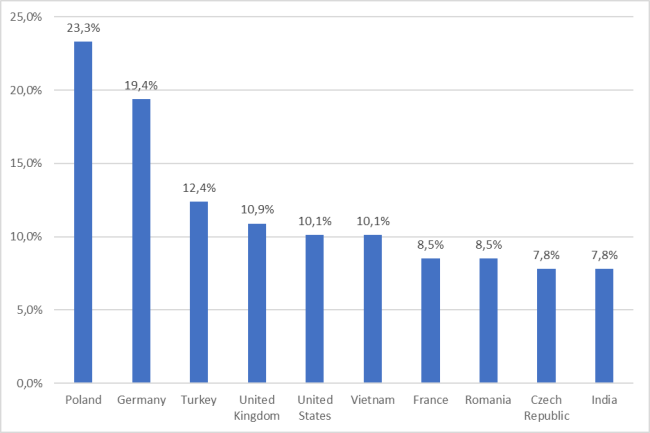
Source: Report by Maersk and Reuter Events – A generational shift in sourcing strategy to dive deeper into near-sourcing, nearshoring and reshoring in the post-pandemic world
How much of this is a passing fad or a desire to build a ‘green image’, and to what extent is it an actual need for companies?
Some companies still see sustainability policy as an image-building opportunity. Especially since usually ‘green solutions’ are simply more expensive and thus unaffordable to smaller companies. Moreover, in many areas we still lack technological solutions that can be applied on a large scale, e.g. in automotive transport we hear from time to time about new alternative fuels, but at the moment these are still in a design phase, covering a fraction of the needs. Despite these challenges, however, we observe that many multinational companies, especially Scandinavian ones, are already ensuring at the tender stage whether a business partner meets their sustainability expectations. Companies in northern Europe place a lot of importance in building green supply chains, often paying more for transport or agreeing to longer delivery times.
We must also not forget that ESG is a social aspect of any business. At SUUS, we care not only about our team, but also about our business partners – haulers and drivers – by offering them an extensive benefits package (e.g. health care, sports cards and discounts at petrol stations) or by creating special zones for drivers in our branches.
Intermodal transport, electric and hydrogen trucks or maybe something else? What will the future of sustainable logistics look like?
Undoubtedly, the future of sustainable TSL industry is intermodal transport. We are also seeing more and more solutions in road transport – hydrogen or electric trucks. However, at the moment, we can only talk about the first pilot projects, testing these solutions out. The preparation of charging infrastructure and the implementation of regulatory solutions for the safe usage of such cars is certainly a major challenge at present.
What is more, we can already see that sustainable logistics will also be based on the ecological design of supply chains, generating the smallest possible carbon footprint. On the one hand, we can achieve this by using the aforementioned environmentally friendly means of transport and, on the other hand, by designing supply chains that introduce all kinds of optimization – according to the customer’s needs – of routes, filling of vehicles or location of distribution centers. At SUUS, we prepare such solutions for our customers as part of our SUUS Advisory service and we are seeing more and more inquiries about them.
That’s transport. And the warehouses? Are they going green?
Although the process of building green warehouses started a few years ago, it has undoubtedly been accelerated by rising energy or gas prices, as well as the turmoil in global markets. The increasing demand for ESG-compliant storage is also an important factor driving the development of this segment. Customers are looking for sustainable solutions throughout the supply chain.
At SUUS, we are committed to green warehouses. Currently, 15 of our 26 facilities are BREEAM-certified, which confirms environmental sustainability and the use of user-friendly solutions. Our newly launched locations include a number of advantages, such as photovoltaic panels, intelligent LED lighting systems, fully-measured areas to continuously monitor our consumption, but also facilities for drivers, such as a rest areas, showers or the possibility to prepare and heat up a meal. We also try to take care of the space around the warehouse by planting flower meadows or putting up insect houses. We also have innovative offices – designed according to the office of the future concept and adapted to the needs of employees (there are, for example, open space areas, conference rooms with modern equipment for online meetings, adjustable desks, acoustic booths or rooms for individual work).
Green = more expensive?
Not necessarily. We can reduce our carbon footprint and costs at the same time. How? At SUUS, as part of the Control Tower service, we combine contract logistics, customs services and all types of freight forwarding, so that we design a comprehensive supply chain and therefore reduce delivery times or transshipments, which has a direct impact on reducing the carbon footprint and costs. In turn, as part of 4PL initiative, we take over planning, analytical and administrative services from our customers, audit transport costs, among other things, and advise on optimal solutions based on our experience.
Is it still possible to save money on supply chains in other ways?
Of course. It all depends on the customer’s needs. For manufacturers in the automotive industry, for example, a good solution is the VMI (Vendor Managed Inventory) service, where the stock of components is managed by a logistics operator together with its supplier at a warehouse located at an optimal distance from the factory. In this model, the manufacturer uses the stock according to his needs and does not bear the direct costs of handling and maintaining it. Payment, as well as costs related to customs and tax issues, can be deferred until the components are taken up. VMI allows production to be optimized and liquidity to be managed more efficiently, which is one of the reasons why we see interest in this service from our customers.
Aleksandra Gumel, Head of Logistics Solution Design CEE, Rohlig SUUS Logistics

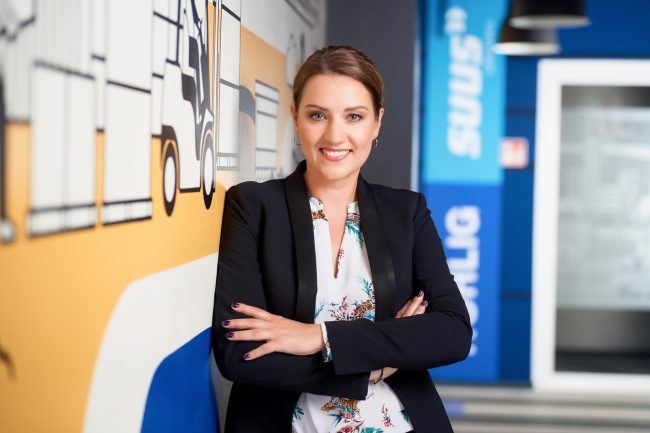
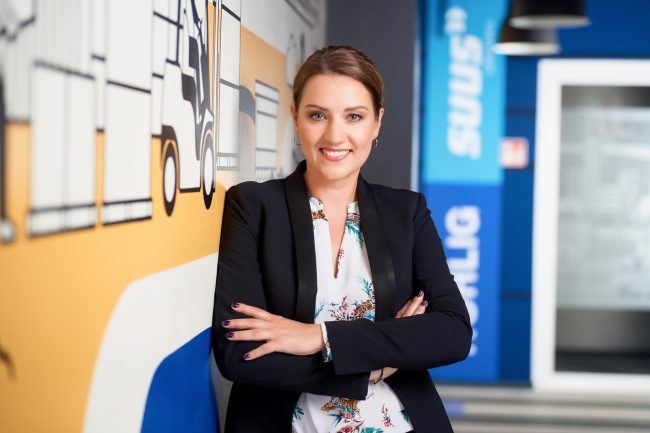
Has been working in the logistics industry for over 15 years. She gained experience in the areas of customer service, project management and contract logistics while working for significant companies in the TSL industry. Since 2017, she has worked for Rohlig Suus Logistics, where she took up the position of Contract Logistics Business Development Manager. Since 2021, she has held the position of Head of Logistics Solution Design CEE. She is a graduate of the Technical University of Lodz and the University of Lodz.
Last Updated on November 24, 2023 by Anastazja Lach