
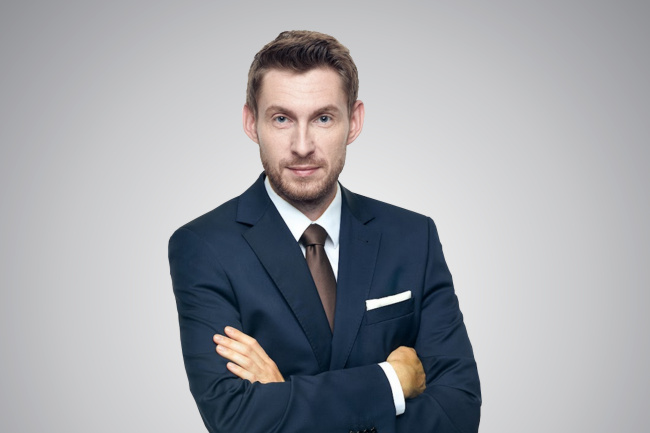
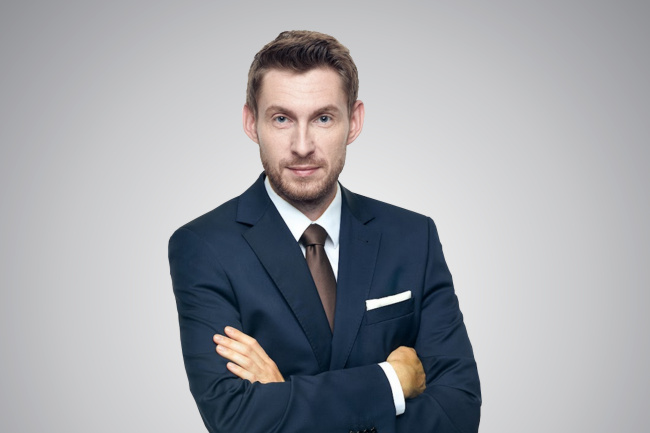
We want to produce cement with a zero carbon footprint by 2027. An interview with Mateusz Piotrowski, Director of Communication and External Relations, Lafarge Poland
Concrete is the second most widely used building material in the world after water. Lafarge has been working for several years to create building materials with a lower carbon footprint. Could you say more about the technology you are using and and it’s impact on the environment on the environment?
That’s right. Concrete is a common material that is, in addition, durable, fireproof, has the ability to store and gradually release heat, and is malleable, allowing the boldest architectural designs to be realized while maintaining their strength. It has one of the lowest carbon footprints in the world, as it typically has 10-15% cement in its composition, is made from natural aggregates and water, and is produced locally and does not need to be transported long distances. Over the life of a building, concrete absorbs 20% of the emissions produced in its manufacture.
There are now low-emission concretes on the market that have a reduced carbon footprint of up to 30%, such as ECOPact concrete. The reduction in CO2 is a result of optimizing the formulation, manufacturing process, and using materials of natural origin that have the lowest carbon footprint, recycled materials and alternative raw materials. Since one of the components of concrete is cement, we want to produce cement with a zero carbon footprint by 2027. We will achieve this through innovative projects, such as a CO2 capture plant at one of our cement plants, which we are working on now.
With this in mind, as well as the versatility of concrete and the fact that it is basically a material that cannot be replaced by an equally effective substitute, it is worth popularizing knowledge about the possibilities of reducing the carbon footprint of buildings through the proper production and use of modern, low-carbon concretes.
Currently, 40% of CO2 emissions within the European Union are generated by construction. The construction sector therefore faces the enormous challenge of reducing the carbon footprint of every square meter of a building through the use of low-carbon materials to increase the energy efficiency of buildings. What technological solutions can help achieve this goal? What are the current barriers to making them widely used?
In order to improve the situation in the European construction industry, it is necessary to conduct research on the carbon footprint produced by buildings and the possibilities of reducing it. In this case, the methodology of life-cycle assessment of products and services called LCA (Life-Cycle Assessment) can help us. This is a systematic approach to assessing the environmental impact of a chosen solution or product. For example, this year, we commissioned the consulting firm SWECO to conduct an independent analysis of the carbon footprint of various concrete mixtures in the structural elements of the aforementioned building. The study showed that the use of our ECOPact concretes for the building’s construction reduced the carbon footprint of the building’s structure by 23%.
In addition, the analysis showed that the highest carbon footprint is produced during the operational phase of the building (the so-called operational carbon footprint). It accounts for more than 70% of the carbon footprint. This is the result of energy consumption such as heating, and is mainly due to poor insulation. It is therefore necessary to ensure better insulation of buildings through the use of appropriate materials, such as insulating foam. This is why it is also important to renovate existing buildings.
Do investments toward so-called green building, i.e. low-carbon materials, carry higher implementation costs? Will operation reduce the costs incurred?
Although these investments may be slightly more expensive, the benefits of their implementation – less environmental impact and reduced operating costs – may outweigh the price of their application. For example, better building insulation reduces heat and energy losses, which will consequently have a positive impact not only on the environment, but also on residents’ wallets. Effective and environmentally friendly insulation is now available on the market. At Lafarge, for example, we produce insulation foam that is fully recyclable.
It should be emphasized that green building also means financial benefits for residents. There are calculations indicating that Poland as a whole could collectively save as much as €17 billion by 2050 through the renovation and thermal upgrading of buildings (VELUX “Healthy Homes Barometer”).
When deciding on a green building, one should make rational estimates of both economic costs and environmental impact. For example – someone may think that the most eco-friendly building material is wood. Meanwhile, importing the right wood from remote areas for construction can, in practice, generate a much higher carbon footprint during transportation than would be generated by using locally produced low-carbon concrete. In addition, the process of producing wood for construction is also energy-intensive and associated with the use of chemicals. In addition, we already have little wood in Poland due to the cutting age of forests. Therefore, it is necessary to save this resource as well, also keeping in mind the issues of CO2 absorption by trees. We should also take into account the rising cost of carbon allowances, which means that the production of traditional, carbon-intensive building materials will decrease. Hence, we should build demand for green solutions. Today they may be more costly than traditional ones, but require less material, are more energy efficient and economical, while also having a lower environmental impact.
How can production be protected against possible power outages? In addition to coal or gas, what feeds or could feed cement plants?
At Lafarge, we emphasize the modernization of our production technology. In recent years, we have made a huge change – we have minimized the use of coal by more than 80 percent in favor of alternative fuels. In addition to our own thermal energy, we still rely heavily on electricity. Therefore, in order to secure production, we are already conducting investment processes towards diversification of energy sources, including, for example, construction of a photovoltaic farm, installation of solar panels.
When it comes to using alternative fuels and power sources, Lafarge is one of the leaders in this field. One of the goals of our Sustainability Strategy is to increase the annual amount of waste used as alternative fuels for heat generation. This will also help reduce their amount in landfills and minimize coal consumption to 0.5 million tons in 2030 (currently 0.4 million tons). The ultimate goal, meanwhile, is to make 100% of the energy consumed by Lafarge plants in 2030 come from renewable and low-carbon energy.
Last year, we announced that a 30MW photovoltaic farm will be built on the site of our cement plant in Wierzbica. From which we will receive all of our energy. This will meet 10% of our cement production needs. At Kujawy and Małogoszcz Cement Plants, installations are being upgraded to support heat recovery from the cement kiln, which will provide clean energy for our plants and meet another 10% of current demand. We are also working on more projects, which we will be announcing soon.
The stagnation of production may bring construction work to a halt. How do you think the coming months will look like in the construction sector? What risks should you pay special attention to?
Cement plants across Europe are currently struggling with rising electricity prices, coal shortages and inflation. All of this will have an impact on the construction market. A lot also depends on the extent to which companies will be helped by high energy costs. Currently, the building materials industry is not on the list of energy-intensive industries. Hence, we are waiting for details and the enactment of a law and then a regulation that will clarify important aspects, including the group of entrepreneurs who will be given assistance. In addition, we estimate that forward market energy price forecasts for 2023 will be above PLN 1,000 per MWh, which will translate into a large increase in production costs and will be felt particularly in energy-intensive industries. Energy costs currently account for almost 50 percent of cement production costs, despite the fact that this is the lowest share in the history of the cement industry.
A major issue that will certainly affect the construction sector is the plans for an emergency tax. The sheer state of uncertainty surrounding this can have a negative impact on investment planning. We do not know, for example, whether the tax will be charged on excess profits or margins, and under what exact conditions. This state of uncertainty is also magnified by the turmoil surrounding the disbursement of funds from the National Reconstruction Plan. Whether Poland ultimately receives these funds will have a very large impact on the dynamics of public investment, which is a significant part of construction work and therefore also shapes the market for the sale of construction materials.
We have already talked about inflation, partly caused by the conflict in Ukraine or the energy crisis. Broken supply chains remain a significant problem. However, it should be remembered that undoubtedly a very important issue for the construction sector in Central and Eastern Europe will be the reconstruction of Ukraine after the war. Let’s hope it happens as soon as possible.
The current economic situation is also affecting demand for construction materials by potentially reducing the number of newly constructed buildings. In recent years, we have had a good boom in residential construction. In 2022, on the other hand, the situation began to deteriorate and the number of transactions fell. According to the latest forecasts, 300-500 thousand refugees from Ukraine may settle in Poland, which will create a demand for 150-200 thousand additional apartments. At that time, the deficit in the housing market may increase by 15-20% in two years. Hence, we can surmise that Poland has the potential to increase the number of housing units under construction, and therefore increase demand for construction materials. However, challenges such as inflation, shortages of raw materials and energy, or administrative barriers must be taken into account.
For now, however, future forecasts are quite cautious. In 2021, 19.3 million tons of cement will be produced in Poland (CSO data), which puts our country in second place in Europe (after Germany and before Italy). Meanwhile, according to estimates, in 2022 Polish cement production will fall to 19 million tons (-1.6% y/y). However, it will already reach 19.4t in 2023, so we expect a recovery. Although the prices of construction materials continue to rise, the growth rate has started to slow down since the spring “top”, which gives hope for an improvement.
An additional opportunity for the construction sector may be one of the goals the European Union plans to achieve; i.e. a wave of renovations. This means that 300 million buildings over the next several years should be modernized in terms of thermal performance. This is a very important project, not only for its potential ability to reduce both energy consumption and CO2 emissions, but also as a driver of sustainable economic growth and job creation in the construction sector.
Mateusz Piotrowski, Director of Communication and External Relations at Lafarge and Vice President of the Lafarge Wspólnie Foundation. Responsible for all corporate online communication and the activities of Public Affairs Lafarge in Poland. Mateusz started his career in leading Polish public relations agencies, conducting corporate, marketing and digital communication activities for a wide variety of clients from the fields of construction, energy, industry and IT. After having moved to Virgin Mobile Polska, he was responsible for all marketing activities on the Polish market. He joined Lafarge in 2019, taking the position of Corporate Communications Manager, and from May 2020 – Communications and External Relations Director. At work, he focuses on open and modern communication based on well-defined company DNA and the use of modern tools for business development.
Last Updated on March 8, 2023 by Anastazja Lach