
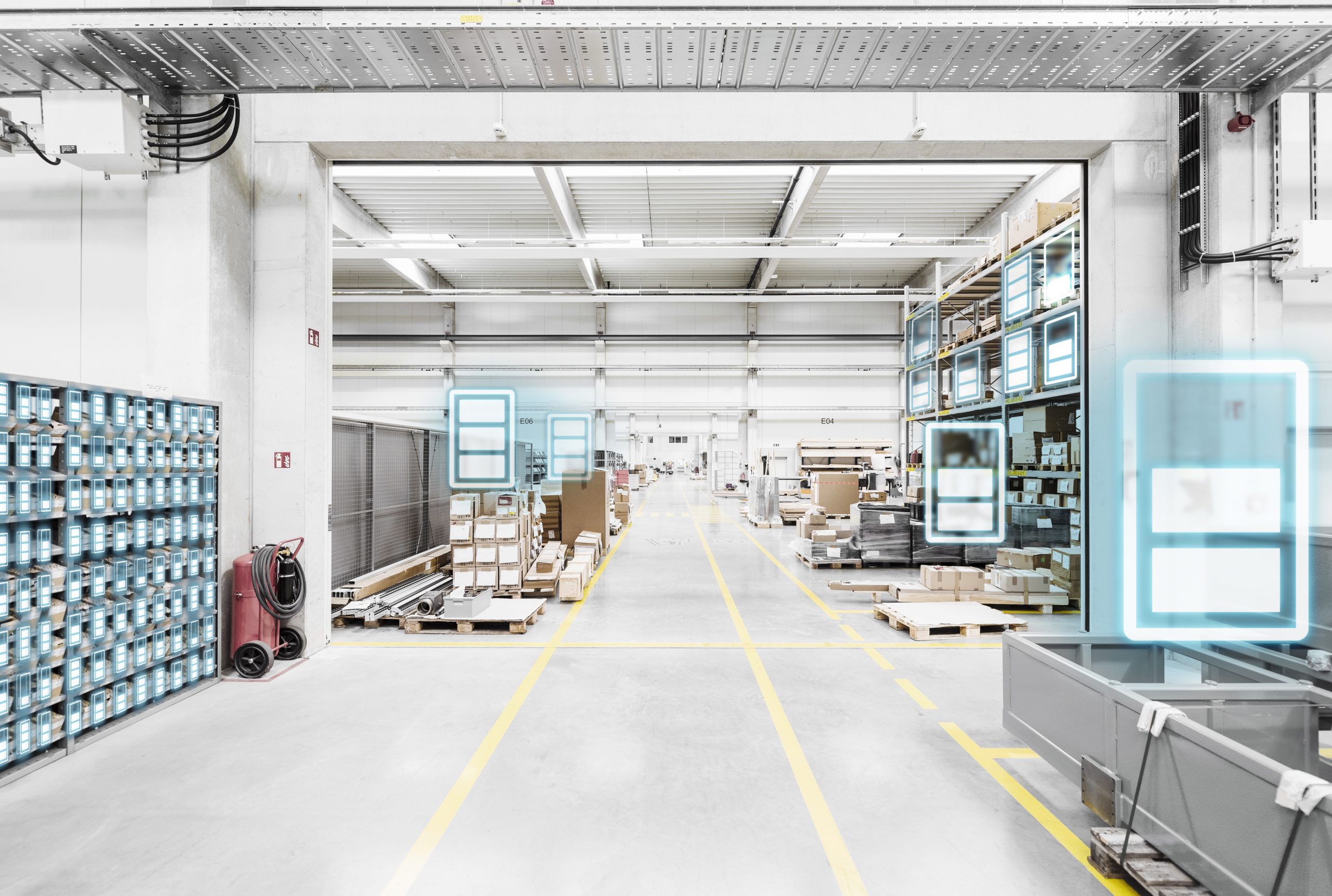
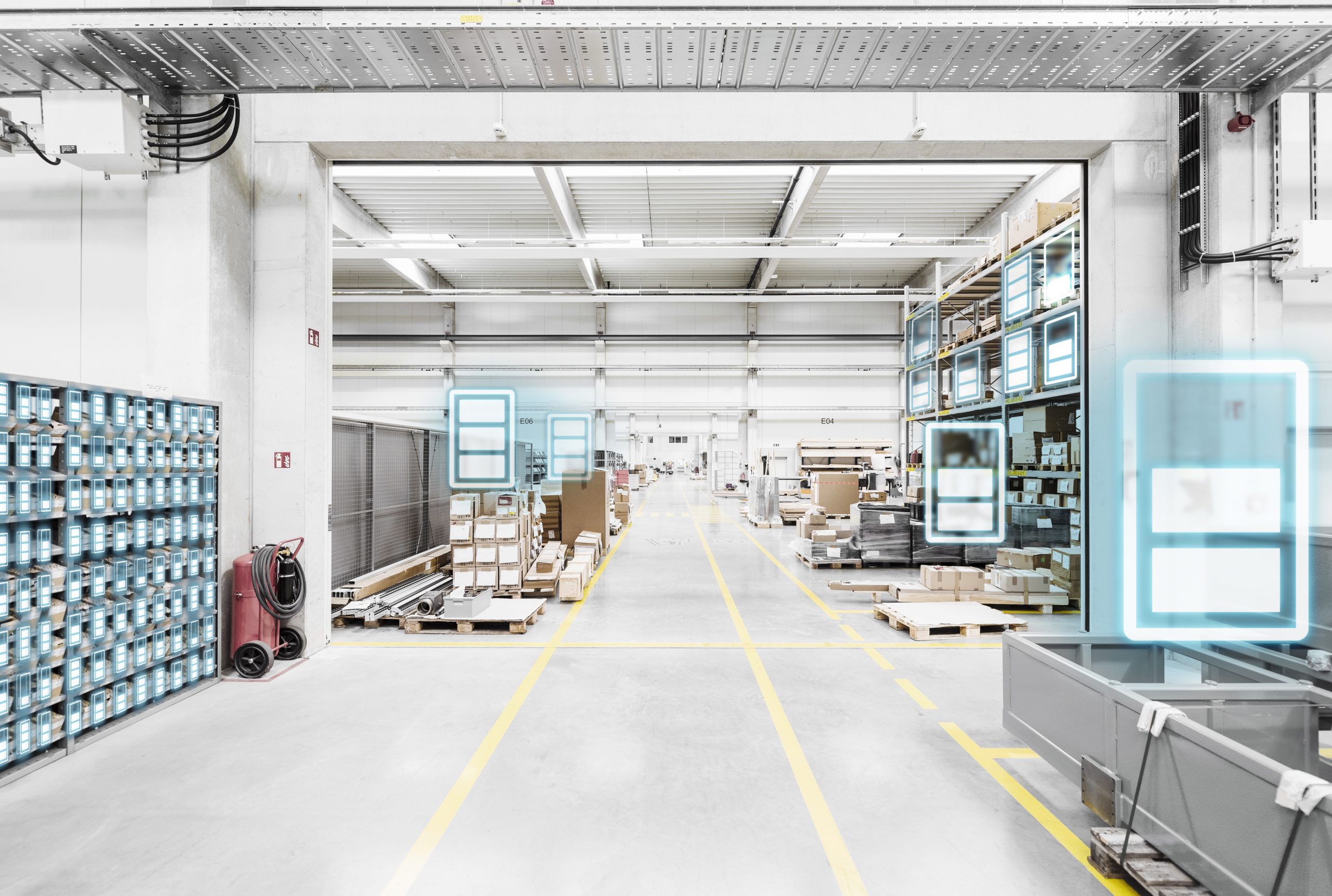
Digitization and Lean Manufacturing – two powerful conceptions in the world of innovation
To be a pioneer, create “that something” which will become a landmark, earning the memory and awe of generations to come… And visionaries, futurologists and innovators are not lacking also in the world of industrial production.
The world races forward. On the one hand, we got used to living in the world of Industry 4.0, although it is not rare that initiatives central to Industry 3.0 are only just being introduced, while on the other hand there are also activities to introduce Industry 5.0 (Community of Practice – CoP 5.0), and there is talk about Industry 6.0.
A moment of reflection brings about these questions: Looking from the perspective of the last three decades and the observable tempo of technological development, are we even entitled to look “so” far ahead? Isn’t our imagination too constricted?
When we hear the word “innovations”, we often think about those so-called breakthrough innovations – large leaps into the future… Which, in fact, are relatively rare, whereas all the while, well within our reach, we have innovations that come up regularly: the so-called radical innovations from the technology perspective, and the so-called supportive innovations from the business perspective (Remigiusz Horbal, LEIP: “Why do good managers “kill” landmark innovations?”).
It is the latter ones, digitization-based, that may be a significant support to Lean Manufacturing principles, allowing to increase productivity, transparency, flexibility, and constant improvement across the whole chain of production value.
In the industrial production sector today challenges are not scarce – they are present in virtually all aspects of conducting a business ‒ and they pertain to such factors as:
- global competition
- disruptions in the supply chain
- technology integration
- deficiencies in staff’s skills
- sustainability and environment protection regulations
Digitization and Lean Manufacturing are two powerful conceptions
Combining them may help increase operational productivity and ensure constant improvement of production processes. It is worth to mention a few important links between digitization and a slimmed-down production:
Decision-making based on data –digitization allows storing, analyzing, and making use of enormous amounts of data from various stages of the production process. The principles of Lean Manufacturing put a stress on decision making based on data and facts, rather than assumptions. This approach allows for taking better decisions, identifies areas that call for improvement, and facilitates constant optimization of processes according to Lean principles.
Process visibility and transparency –digitization enhances visibility and transparency across the whole chain of production value, providing real-time oversight of production operations, supply levels, and supply chain dynamics. Lean Manufacturing stresses techniques of visual management, such as Kanban boards, process maps and productivity dashboards, so that all information is easily accessible and comprehensible to everyone. By digitizing these tools and integrating them into the data flux from various sources, manufacturers may create their own digital ecosystem that fosters transparency, facilitates communication, and enables a proactive problem solving, thus following Lean principles.
Flexible and efficient operation – digitization ensures a greater flexibility and efficiency in production operations, allowing companies to react promptly to the changing requirements of clients, the shifting market conditions and production demands. Lean Manufacturing is for flexible production systems that may be adjusted to various sizes of production and product ranges with no loss in efficiency nor quality. Through implementing digital technologies, such as advanced robotics, additive production and flexible automation systems, manufacturers may achieve greater flexibility in production planning, resource allocation, and processes reconfiguration. This flexibility complies with Lean principles regarding loss minimization and maximization of added value operations, through ensuring efficient use of resources.
Constant improvement and innovations – digitization speeds up the tempo of constant improvement and innovation, providing tools and platforms for experimentation, simulation, and rapid prototyping. Lean Manufacturing fosters a culture of constant improvement through practices such as Kaizen, and value stream mapping. Thanks to integrating such digital tools as simulation software, digital twins, and collaboration platforms, manufacturers may test new ideas, simulate changes in their processes, and involve their staff in problem solving and innovative initiatives in a more efficient way. This synergy between digitization and Lean principles favors a culture of innovation, experimentation and learning, thus driving constant improvement in production processes and products.
Focus on the client and building values – digitization allows manufacturers to focus on the clients more by storing information about their preferences, behaviors and needs, and translating those into added value products and services. Lean Manufacturing stresses delivering value to the client, by focusing on operations that have direct impact on fulfilling the clients’ demands while minimizing losses. This approach is in accordance with Lean principles that focus on creating value, stimulate competitiveness and sustainable growth in the digital industry of today.
Innovations in practice
Despite increasing awareness, there are still concerns about implementing innovations, specifically with such factors as the costs and time of return on investment, period of implementation, benefits, interference in the production process, staff qualifications, or finally, maintaining the status quo, often mistaken for stability.
These concerns are addressed by technology providers who, like Balluff, use the Lean Startup methodology in their own operation, creating solutions dedicated to selected areas in order to allow users to achieve substantial benefits within a short time-span. Moreover, these solutions are independent from users’ control systems; they are based on process digitization, integrate the OT and IT spheres, and provide practical support for Lean Manufacturing.
Selected innovations, although available for implementation in manufacturing conditions, are constantly developed and amended with new functionalities for specific areas:
- Condition Monitoring Toolkit (CMTK) ‒ monitoring of the condition of machines and installations
- Smart Reordering System (SRS) ‒ automatized supply management – dynamic and smart
- Guided Changeover Solution (GCS) ‒ partial automation of the machine changeover process
- Asset Data Provider (ADP) ‒ an integrated Software-as-a-Service (SaaS) solution, OT and IT integration
- RadarImager – detection of concealed objects to boost quality assurance
Integrating digitization and Lean Manufacturing makes it possible for manufacturers to optimize processes, increase flexibility, support innovation, and deliver greater value to the clients, thus enhancing operational excellence. Therefore, implementing innovations is no longer a choice, but rather a necessity, allowing to maintain competitiveness in the ever more digital and dynamic landscape of production.

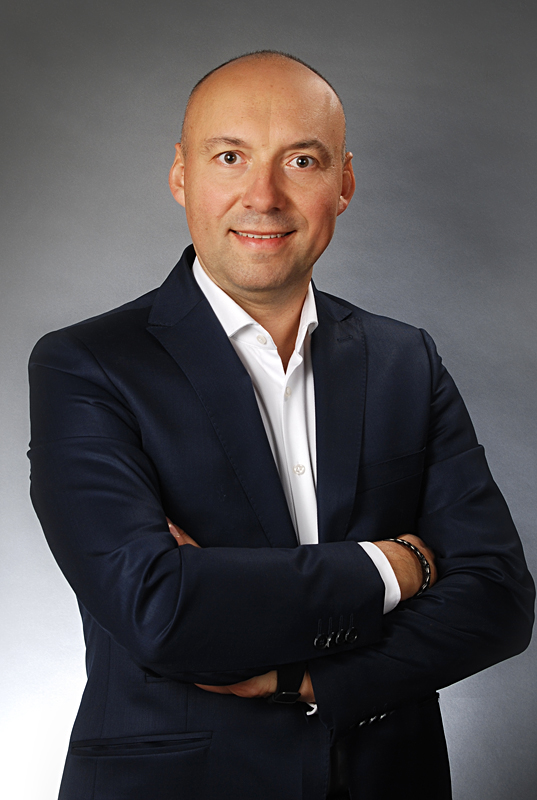
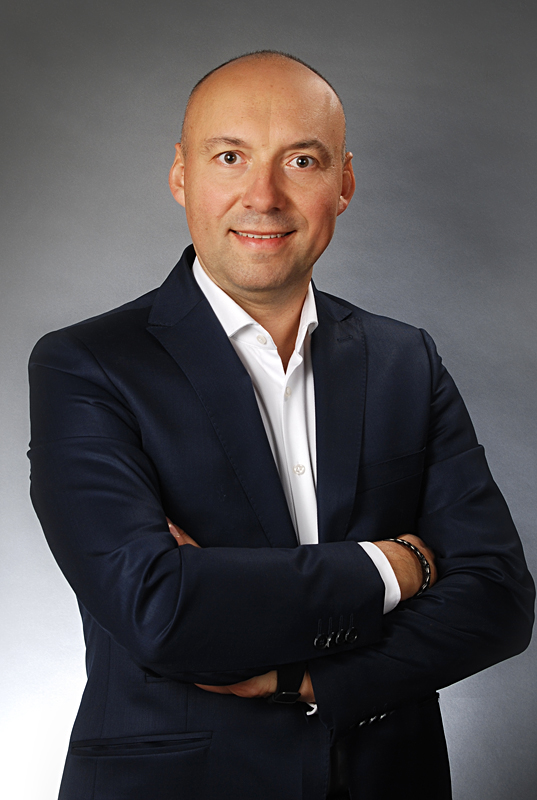
PAWEŁ JURAS
Business Development Manager EMEA, Balluff EMEA
Last Updated on March 22, 2024 by Anastazja Lach