
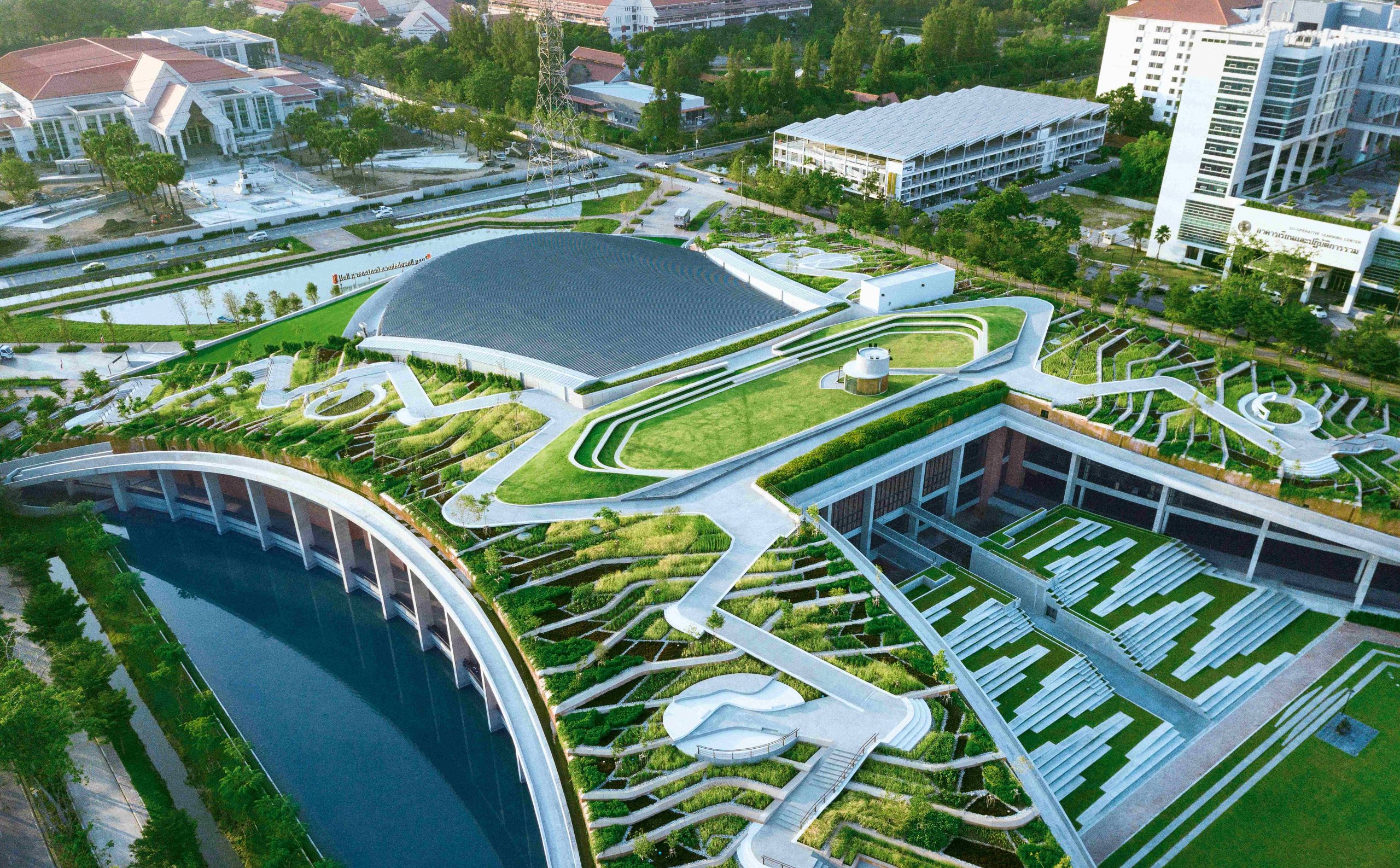
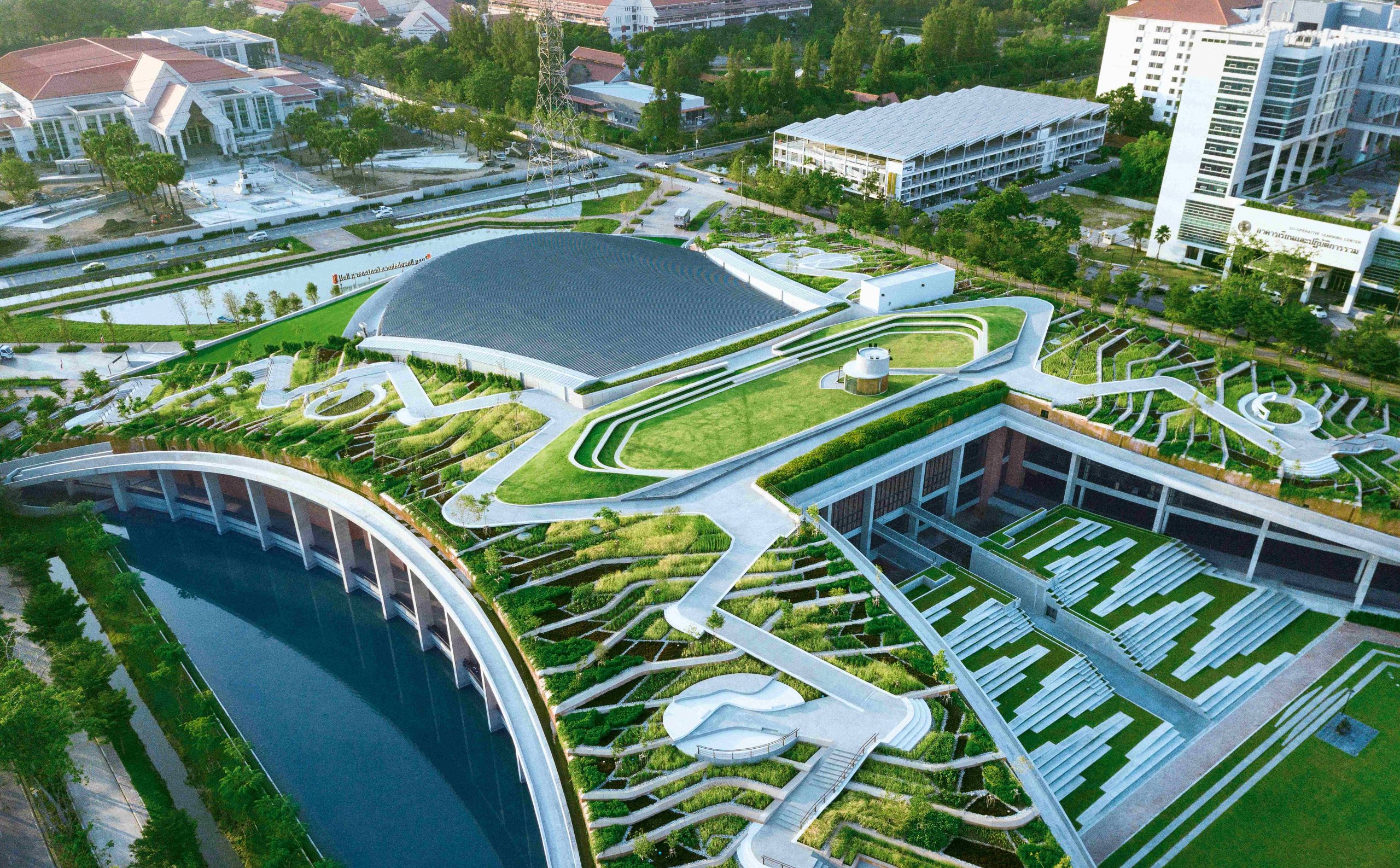
Sustainable urban development accelerates – infrastructure and buildings made of recycled materials
The construction sector accounts for 38 percent of CO2 emissions in the European Union. That is why it has been included as one of the eight priorities of the Green Deal strategy. This shows how much importance we must place on the construction process and the materials used to build our cities.
The dynamic growth of cities due to ongoing climate and socioeconomic changes is now unstoppable. The consequence of this is an increase in human migration, which forces further investment in infrastructure development and housing. We already know that the deficit in the housing market is estimated at 1.5-2 million housing units, with a tendency to increase in the coming years. Hence, cities must expand accordingly.
Circular economy as an important factor in green transformation
Sustainable urban development depends on the sustainability of the construction industry, which is increasingly adopting a circular economy model. Significant progress in the green approach has been made by the cement industry, which in recent years has strongly developed the use of waste in the production of building materials. Lafarge in Poland, which is part of the Swiss Holcim Group, has made progress. Lafarge in Poland processes 1.8 million tons of various types of waste, using it in cement production. Of these, 0.4 million tons is non-recyclable waste from, among other things, municipal waste. They are used to produce alternative fuel used to generate heat in the cement clinker. At the same time, this waste ends its life in an irrevocable, and importantly, emission-free way, instead of lying in landfills. This action allows today to replace 80 percent of coal in the company’s production processes. The remaining 1.2 million tons are waste from other industries such as ash, slagand by-products of combustion, which Lafarge uses as raw materials for cement production, reducing the amount of clinker in cement that comes from firing hard coal. Consequently, this translates into accelerated decarbonization processes.
– Last year, as Lafarge, we launched cement under the ECOPlanet brand, which can have up to a 50 percent lower carbon footprint than traditional cement, precisely due to the use of alternative raw materials that are also decarbonized. On its basis, ECOPact sustainable concrete is created, suitable for buildings and infrastructure created in the eco-concept – said Maciej Sypek, General Director of Cement Sales and Logistics, Lafarge in Poland.
With a view to the comprehensive management of mineral raw materials, Lafarge in Poland is creating a special ARM platform at the Kujawy Cement Plant. The platform’s task will be to properly prepare raw materials and industrial waste for clinker production. These will include, among others, ash and slag, lime waste from water decarbonization, and lime waste from cellulose production. Materials that are wasted for many industries will get a second life in cement production. The platform will take the form of a separate installation where raw materials will be prepared for production at the cement plant.
Building better with less
The recycling of building materials, which Lafarge also uses, is part of the urban mining trend. It assumes that unused urban areas are seen as repositories for raw materials that can be reused to make building materials. These raw materials are employed to create recycled aggregates that are produced close to the site of newly constructed buildings. This gives recycled aggregates a logistical advantage over natural aggregates mined at specific locations. At the same time, it involves minimizing environmental impact and reducing the use of natural rock from where the aggregate is originally mined.
Following the principle of “build better with less,” Lafarge plans to reduce the use of mined aggregate in favor of selected aggregate from demolition. By 2030, the company wants to bring more than 1 million tons of recycled aggregates to the market. This approach addresses today’s challenges of both accessing and reducing the use of natural resources, as recycled aggregate finds reuse in infrastructure or as an additive to concrete.
One example of urban mining is the demolition of the old Krakow Nowa Huta Cement Plant. Lafarge converted the rubble into full-grade aggregate through a process involving strict inspection, selection, and cleaning from other materials. In addition, the recycled aggregate is more than 20 percent lighter than natural aggregate at the same parameters. Using the example of the realization in Krakow, Lafarge specialists calculated that the supply of this aggregate reduced CO2 emissions in transport by 66 percent and by as much as 74 percent in emissions per m3 of work performed compared to aggregate from nearby mines.
– In pursuit of circularity, Lafarge seeks sources of materials in various places. Sourcing materials in an environmentally friendly way requires outside support and expertise. That’s why we are working on a project for a comprehensive solution to the problem of construction waste in the largest Polish agglomerations. The idea is to give demolition materials a second life – explained Hubert Krysiak, Construction Materials Recycling Manager, Lafarge in Poland. Lafarge is taking further steps in lowering its CO2 emissions and introducing sustainable solutions dedicated to green building. The circular economy is at the heart of our business operations, and every year we do more to use less!

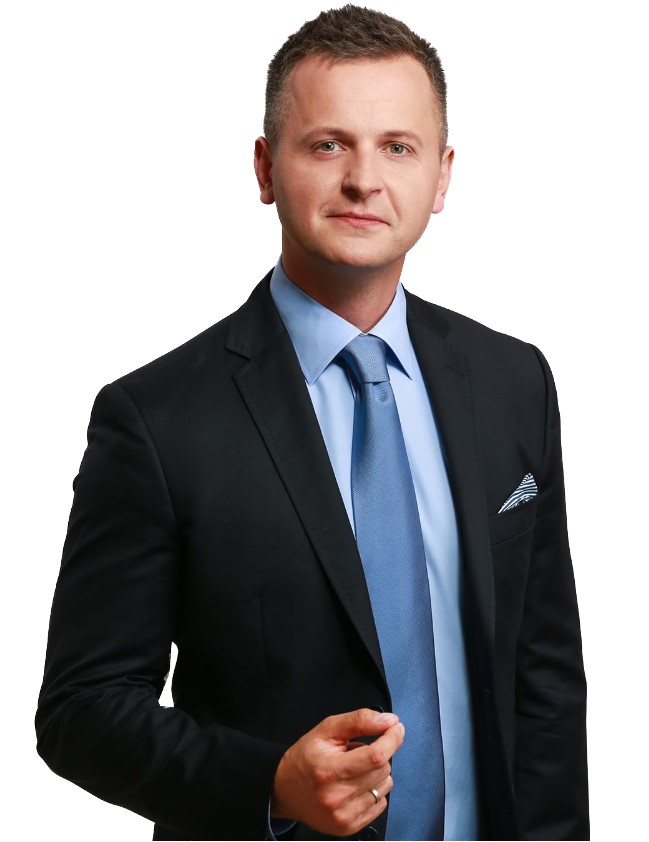
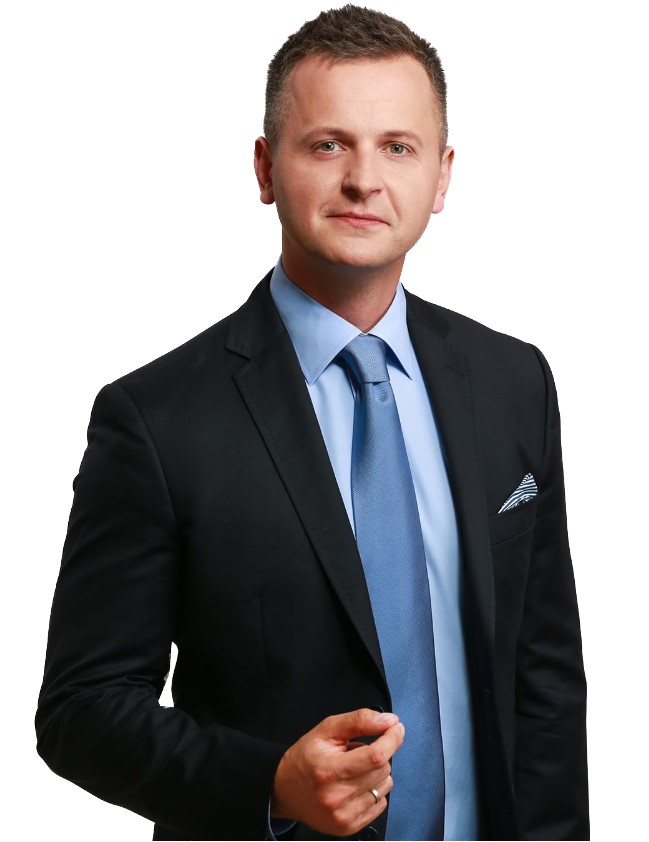
Maciej Sypek, General Director of Cement Sales and Logistics, Lafarge in Poland

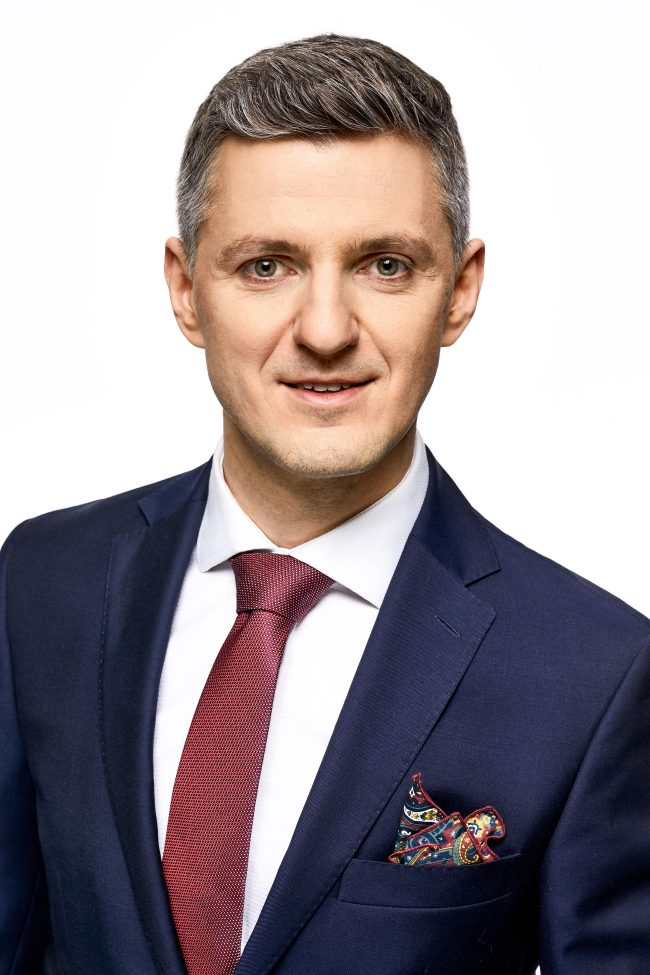
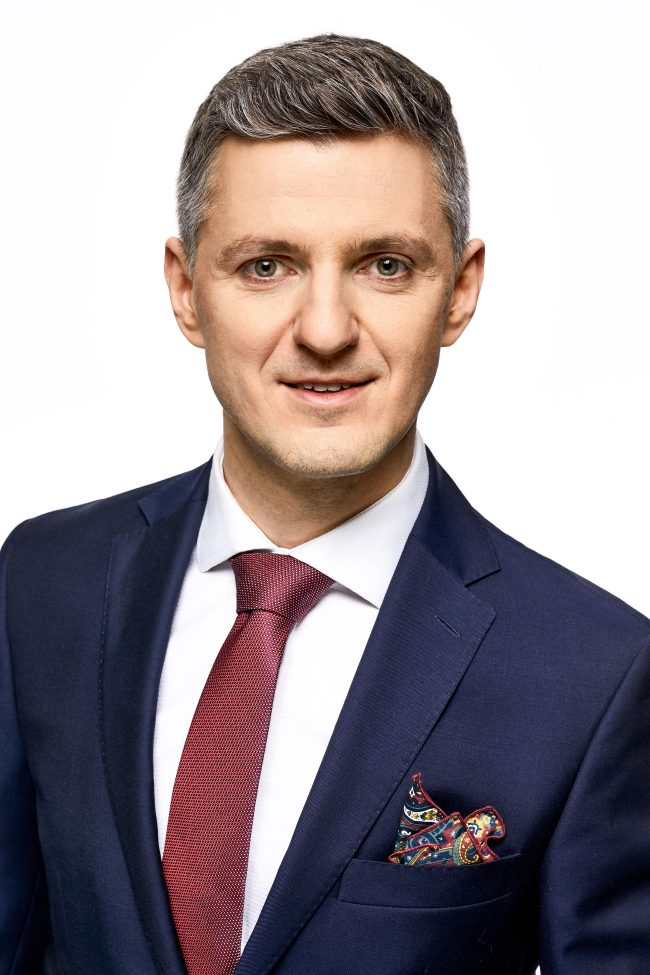
Hubert Krysiak, Construction Materials Recycling Manager, Lafarge in Poland
About Lafarge in Poland
Lafarge is the world leader in innovative and sustainable building solutions.
We create environmentally friendly products and solutions such as ECOPact – the concrete with almost 50% less carbon footprint than standard ready-mix concrete; green cements with 30-50% less carbon footprint than pure Portland cement CEM I; and many others. We use recycled resources and recycled raw materials in our production processes. Lafarge in Poland is part of the global Holcim Group which employs around 70,000 people in 70 countries in four segments: Cement; Concrete; Aggregates; Solutions and Products. Holcim supports the creation of more sustainable and greener cities, and helps to develop smart infrastructure and improve living standards around the world.
For more information please visit: www.lafarge.pl; www.holcim.com
Last Updated on June 16, 2023 by Anastazja Lach